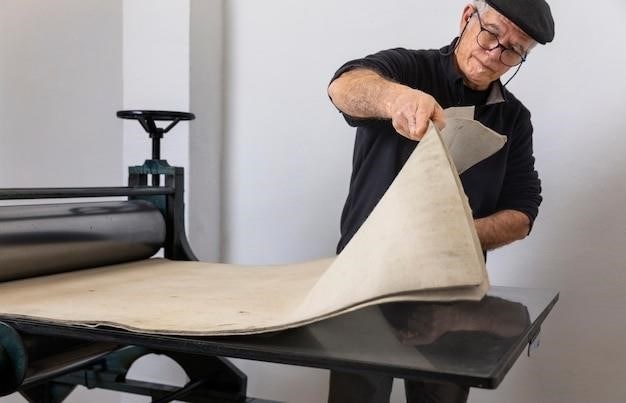
Introduction to Manual Heat Presses
Manual heat presses are essential tools for transferring designs onto various surfaces, including T-shirts, mugs, hats, and more․ These presses are operated by hand, providing precise control over pressure and time․ They are a versatile and affordable option for individuals and small businesses looking to personalize items or create custom merchandise․
What is a Manual Heat Press?
A manual heat press is a device used to transfer images, designs, or text onto various surfaces using heat and pressure․ Unlike automatic presses, which rely on a hydraulic system, manual presses require the user to apply pressure using a lever or handle․ They are typically used for smaller projects and offer a more hands-on experience․
The basic components of a manual heat press include a heating element, a pressure plate, and a base plate․ The heating element generates the heat needed to transfer the design, while the pressure plate applies even pressure to the surface․ The base plate provides a stable platform for the item being pressed․
Manual heat presses are often used for smaller projects, such as customizing T-shirts, mugs, hats, and other items․ They are also a popular choice for craft enthusiasts and small businesses looking to create unique and personalized products․
Types of Manual Heat Presses
Manual heat presses come in various designs, each catering to specific needs and applications․ Here are some common types⁚
- Swing-Away Heat Presses⁚ These presses feature a hinged upper platen that swings away from the base, allowing for easy access to the pressing area․ This design makes it convenient for placing and removing items․
- Clamshell Heat Presses⁚ Clamshell presses have a top platen that closes down onto the base plate like a clamshell․ They offer a more compact design and are often used for smaller items․
- Pillow Heat Presses⁚ Pillow presses have a flat heating element that sits on a base plate․ They are typically used for pressing flat surfaces like T-shirts or fabric panels․
- Specialty Heat Presses⁚ These presses are designed for specific applications, such as pressing mugs, caps, or plates․ They often feature specialized platens and attachments․
The choice of manual heat press depends on the type of items you plan to press, the size of your projects, and your budget․ Researching different models and features will help you find the perfect fit for your needs․
Using a Manual Heat Press
Operating a manual heat press is straightforward but requires careful attention to safety and proper technique to achieve successful transfers․
Safety Precautions
Before using a manual heat press, it’s crucial to prioritize safety to prevent accidents and ensure a smooth experience․ Always unplug the press from the power source when not in use, and ensure the surrounding area is clear of flammable materials․ Never leave the press unattended while it’s heated․ Exercise caution when handling the hot platen, using heat-resistant gloves to prevent burns․ Additionally, avoid wearing loose clothing that could catch on the press, and ensure proper ventilation to dissipate heat and fumes․ Following these safety guidelines will create a safe and secure environment for operating your manual heat press․
Setting Up the Heat Press
Setting up your manual heat press is a straightforward process that involves a few essential steps․ Begin by placing the press on a stable and level surface, ensuring adequate space around it for easy access and movement․ Connect the press to a dedicated power outlet and ensure the power cord is properly secured․ Turn on the press and allow it to preheat to the desired temperature, as specified in the manufacturer’s instructions․ While the press is heating, prepare your work area by laying down a heat-resistant mat or a piece of plywood to protect your workspace from potential heat damage․ Once the press reaches the desired temperature, you’re ready to begin the transfer process․
Preparing the Transfer
Before applying the transfer to your chosen substrate, it’s crucial to prepare it properly․ Begin by carefully removing the transfer design from its backing sheet, ensuring that it is intact and free from any imperfections․ Place the transfer design face-down on the substrate, ensuring it is positioned correctly and centered according to your design․ If using a heat transfer tape, apply it to the back of the transfer design to secure it and prevent it from shifting during the pressing process․ Make sure the tape is firmly adhered to the transfer, especially around the edges, and remove any air bubbles that may have formed․ Once the transfer is securely in place, you’re ready to begin the pressing process․
Applying the Transfer
With the prepared transfer design in place, it’s time to apply it using your manual heat press․ Lower the heated platen of the press onto the transfer design, ensuring even pressure is applied across the entire surface․ The pressure should be firm but not excessive, as too much pressure can damage the transfer or the substrate․ Maintain the pressure for the specified amount of time, as indicated by the manufacturer’s instructions for your specific transfer type and substrate․ This time will vary depending on the type of transfer and the material you’re working with․ Once the pressing time is complete, carefully lift the platen, being sure to avoid any sudden movements that could cause the transfer to shift or become misaligned․
Cooling and Peeling
After applying the transfer and lifting the heat press platen, allow the design to cool completely․ This is a crucial step, as it allows the adhesive in the transfer to set properly and prevents the design from lifting or peeling prematurely․ The cooling time will vary depending on the type of transfer and the substrate, but generally, it’s best to wait at least 30 seconds to a minute before peeling away the carrier sheet․ Once the transfer has cooled, carefully peel away the carrier sheet, starting from a corner and slowly pulling it back in a smooth motion․ If the transfer resists peeling easily, it may not be fully adhered․ If this happens, you can gently apply some pressure to the transfer while peeling to ensure it’s securely attached․
Troubleshooting Common Problems
Even experienced heat press users encounter occasional challenges․ This section addresses common issues and provides solutions to help you achieve successful transfers․
Heat Press Not Heating Up
A heat press that fails to reach the desired temperature can be frustrating․ Here are some common causes and solutions⁚
- Check the Power Cord and Outlet⁚ Ensure the power cord is securely plugged into a working outlet․ If the outlet is faulty, try another one․
- Inspect the Fuse or Circuit Breaker⁚ A tripped fuse or circuit breaker can prevent power from reaching the heat press․ Check your electrical panel and reset any tripped components;
- Verify the Temperature Setting⁚ Double-check that the temperature is set correctly and that the heat press is turned on․ Some models have a separate power switch and a temperature control knob․
- Clean the Heating Element⁚ Dust or debris accumulating on the heating element can hinder heat transfer․ Unplug the heat press and clean the element with a damp cloth․
- Check the Temperature Sensor⁚ A faulty temperature sensor can prevent the heat press from accurately reading the temperature․ Contact the manufacturer or a qualified technician for assistance with this issue․
If you’ve followed these steps and your heat press still isn’t heating up, it’s best to consult the manufacturer’s instructions or contact their customer support for further guidance․
Uneven Pressure
Uneven pressure during the heat pressing process can lead to inconsistent transfer results, with some areas adhering properly while others don’t․ Here’s how to troubleshoot and address uneven pressure⁚
- Check the Pressure Adjustment Knob⁚ Most manual heat presses have a pressure adjustment knob․ Ensure it’s properly calibrated and adjusted to the correct pressure for your project․
- Inspect the Platen Surface⁚ Uneven platen surfaces can cause pressure inconsistencies․ Check for any dents, scratches, or warping that might affect the pressure distribution․
- Use a Pressure Gauge⁚ A pressure gauge can help you accurately measure the pressure being applied․ If the gauge readings are inconsistent, it might indicate a problem with the pressure mechanism․
- Ensure Proper Placement of the Transfer⁚ Make sure the transfer is centered and positioned correctly on the substrate․ Incorrect positioning can result in uneven pressure distribution;
- Use a Heat Press Mat⁚ A heat press mat provides a more even pressure distribution and helps protect the substrate from direct heat․
If you continue to experience uneven pressure, it’s advisable to contact the manufacturer or a qualified technician for assistance․
Transfer Not Adhering
If your heat transfer design isn’t adhering properly to the substrate, it can be frustrating and lead to wasted time and materials․ Here’s a breakdown of common causes and solutions for this issue⁚
- Incorrect Temperature and Time Settings⁚ Every transfer material has specific temperature and time requirements․ Ensure you’re using the correct settings for your chosen transfer type․ Consult the manufacturer’s instructions or a heat press guide for accurate settings․
- Insufficient Pressure⁚ Insufficient pressure during the heat pressing process can prevent the transfer from fully adhering to the substrate․ Check your pressure settings and ensure they are adequate for your project․
- Transfer Material Issues⁚ The transfer material itself could be faulty or expired․ Ensure you’re using fresh, high-quality transfers․
- Substrate Compatibility⁚ Not all transfer materials are compatible with all substrates․ Verify that the transfer you’re using is compatible with the material you’re applying it to․
- Surface Contamination⁚ Dirt, oil, or moisture on the substrate can interfere with the transfer adhesion․ Clean the surface thoroughly before applying the transfer․
By addressing these potential causes, you can troubleshoot transfer adhesion problems and achieve successful heat press results․
Maintenance and Care
Regular maintenance and care are crucial for ensuring your manual heat press operates smoothly and delivers consistent results․
Cleaning the Heat Press
Keeping your manual heat press clean is essential for maintaining its performance and extending its lifespan․ After each use, allow the press to cool down completely before cleaning․ Use a soft, damp cloth to wipe away any residue or debris from the heating platen, base plate, and surrounding areas․ Avoid using abrasive cleaners or solvents as they can damage the surfaces․
For stubborn stains, a mild soap solution can be used․ Apply the solution to a cloth and gently rub the affected areas․ Rinse the cloth thoroughly and wipe down the press again with a damp cloth․ Ensure all cleaning solutions are completely dried before using the press again․
Regular cleaning helps prevent buildup and ensures even heat distribution during the pressing process․ Always refer to the manufacturer’s instructions for specific cleaning recommendations for your model․
Replacing Parts
Over time, wear and tear on your manual heat press may require replacing certain parts․ This ensures optimal performance and safety․ Common parts that may need replacement include the heating element, pressure pads, and control knobs․ Check your manufacturer’s manual for a parts diagram and information on identifying and replacing specific components․
When replacing parts, always use genuine parts from the manufacturer or a reputable supplier․ Using non-compatible parts can lead to malfunctions and damage to your press․ Before replacing any parts, ensure the press is unplugged and completely cool․ Follow the manufacturer’s instructions carefully and exercise caution when handling any electrical or mechanical components․
By replacing worn parts promptly, you can extend the life of your manual heat press and ensure consistent, reliable performance for your projects․
Manual heat presses offer a simple and effective way to create personalized and customized items․ With proper care and maintenance, they can be a valuable tool for individuals and businesses alike․
Benefits of Using a Manual Heat Press
Manual heat presses offer several advantages over their automated counterparts, making them a popular choice for various applications․ Their affordability is a significant benefit, making them accessible to individuals and small businesses with limited budgets․ Manual presses provide precise control over pressure and time, allowing users to achieve optimal results for different materials and designs․ This precision is crucial for delicate items or intricate patterns, ensuring a high-quality transfer every time․ The compact size of manual presses makes them easy to store and transport, ideal for home-based businesses or mobile operations․
Choosing the Right Manual Heat Press
Selecting the appropriate manual heat press depends on your specific needs and the types of projects you plan to undertake; Consider the size of the press, as it determines the dimensions of the items you can transfer designs onto․ The pressure capabilities of the press are crucial, as it affects the quality and adhesion of the transfer․ Look for a press with adjustable pressure settings to accommodate various materials and thicknesses․ The temperature control system should be accurate and reliable, ensuring consistent heat for optimal transfer results․ Additionally, consider features like a timer, pressure gauge, and safety features to enhance your experience and ensure safe operation․